7. 膨胀节性能测试 7.1 试验目的及规则
膨胀节是一个承受内压和位移载荷的弹性元件,不但要求其具备设计所要求的功能,而且应该能保证安全地工作,显然,这是十分重要的。为了考核有关的力学性能和安全性。必须进行有关的性能试验。特别是在下列情况,更有必要进行试验:当新产品投产;产品正式生产后因其结构、材料、工艺有较大改变且可能影响膨胀节的性能时;长期停产后恢复生产;劳动部门进行制造资格认证或质量监督机构要求进行质量检查时都要做一系列的性能试验。试验的主要项目有:耐压试验、气密试验、应力测定、刚度测定、稳定性试验、疲劳试验和爆破试验等。所有试验都应遵循国家或行业的有关标准与技术条件的要求,也可参考国外有关标准和技术条件。
7.2
试验项目及技术要求 1)耐压试验
膨胀节产品在出厂前,都要按规定进行耐压试验。试验的目的是检验膨胀节在超工作负荷条件下的宏观强度,检验它是否具备在设计载荷下安全运行的能力,同时,可检验膨胀节的致密性,检查材料、结构和制造工艺中可能存在的问题。
耐压试验时,要求两端用盲板密封,还要将两端固定,便之在压力试验时不得伸长,一般情况下,是用坚固的拉杆拉紧两端盖。同时要测量各波间的波距。
1)液压试验
液压试验时,试验压力按式(68)和式(69)计算,取其中的小值。
PT=1.5P[σ]/[σ]t
(68)
PT=1.5PscE/Et
(69)
式中:PT试验压力,Mpa;
P(内压或外压的)设计压力,Mpa;
[σ]、[σ]t分别为试验温度和设计温度下波纹管材料的许用应力,Mpa;
E、Et分别为试验和设计温度下波纹管材料的弹性模量,MPa;
Psc为柱失稳极限设计压力,Mpa;
外压式膨胀节按式(68)决定试验压力。
进行耐压试验时,应注意检查波纹管波距的变化,在试验压力下,对于不带加强环(或稳定环)的膨胀节,受压时最大波距与受压前波距之比不得大于1.15;对于带加强环的膨胀节,受压时最大波距与受压前波距之比不得大于1.20。如果经过分析不能保证膨胀节在试验压力下波距的变化限制在规定范围内,可考虑适当降低试验压力,最后是否降压试验,须由技术负责人决定。
液压试验时,可用室温水作试验介质。对奥氏体不锈钢波纹管膨胀节,试验用水的氮离子含量应不越过25ppm。试验时,压力应缓缓上升,当加压至设计压力后,压力应逐级增加,每级压力级差不超过试验压力的10%,一直升压至规定的试验压力,并保压10分钟,此时,各连接部位和焊缝处应无渗漏、无异常变形和异常的响声,并测量波距,分析波距的变化,判断其是否发生过失稳现象,并作出质量结论。试压情况及结论应及时记录在试验报告上,试验结束后,应排尽水,并擦干净膨胀节内外表面的水渍。
在耐压试验中,要注意到试验介质的温度和环境温度,因为,当试验温度低于材料的脆性转变温度时,有可能导致材料发生低应力脆断事故。为安全起见,参照《压力容器安全监察规程》的规定,当端管、中间管和法兰为碳素钢和16MnR钢制造时,试压时的水温和环境温度不应低于5℃,当为其它低合金钢时(不包括低温用钢),控制温度不低于15℃。其它材料制膨胀节的耐压试验温度按图样设计规定要求。
在进行水压试验前,应进行必要的强度校核,使波纹管和有关接管的一次总体薄膜应力值不得超过所用材料在该试验温度下屈服点的90%。若强度校核不合格,由技术负责人处理,可作出降压试验的决定。
在液压试验过程中,首先应将膨胀节内部充满水,排净滞留在膨胀节内的气体,静置一段时间,待膨胀节壁温与液体介质温度相同后方才升压。
试验过程中,必须保持膨胀节外部表面干燥、清洁。
试验过程中所用压力表应在检验有效斯内,其最大量程为试验压力的1.5-3倍。精度应符合要求,对低压情况精度不低于2.5级,对中压情况,精度不低下1.5级。并应安装在显著位置。
2)气压试验
当膨胀节由于结构复杂,液压试验不足以反映出各点试压要求,或因其它原因不适合进行液压试验时,可考虑进行气压试验。
试验压力按式(70)和式(71)计算,并取其中的较小值。
PT=1.1P[σ]/[σ]t
(70)
PT=1.1PscE/Et
(71)
式中符号意义同式(68)和式(69)。
进行气压试验时,现场必须有可靠的安全防护措施。进行气压试验的膨胀节,其主要焊缝应进行100%的无损探伤检测。
气压试验介质一般为干燥、清洁的空气,也可以是氮气或其它惰性气体。
试验温度也同样有一定要求,当接管等为碳素钢和低合金钢制膨胀节,试验用气体温度不得低于15℃,对于其它材料,则根据图样耍求。
试压过程中,首先缓馒升压至规定试验压力的10%,保压5一10分钟,并对所有焊缝和连接部位进行初次检查,若无泄漏,可继续升压至规定试验压力的50%,若无异常情况,其后,按每级为规定试验压力的10%逐级升压到试验压力,保压10分钟,此间压力应保持不变。不得采用连续加压的方法维护压力。不得在有压力的情况下紧固螺拴。经肥皂液或其它方法检漏。无漏气,无可见异常变形为合格。
(2)气密试验
膨胀节气密试验的主要目的是检验焊缝及各个可拆连接密封部位的致密性和密封性,以保证膨胀节在工作条件下严密不漏。在工程上,并非所有膨胀节都要进行气密性试验。根据规定,只有当工作介质为易燃易暴或为中度危害以上时,真空条件下操作且真空度大于0.085Mpa时或对泄漏有特殊要求时,才进行气密试验。
所谓易燃介质是指与空气混合的爆炸下限小于10%,或爆炸上限和下限之差值大于等于20%的气体,如--甲胺、乙烷、乙烯、氯甲烷、环氧乙烷、环丙氢烷、丁烷、三甲胺、丁二烯、丁烯、丙烷,丙烯、甲烷等。
所谓中度危害介质,是指最高允许浓度为1.0--10mg/m3的介质,这是根据GB5044《职业性接触毒物危害程度分级》的规定。按规定危害程度分四级,其中中度危害为Ⅲ级。极度危害为I级;中度危害介质如:二氧化硫、氨、一氧化碳、氯乙烯、甲醇、氧化乙烯、硫化乙烯、二硫化碳、乙炔、硫化氢等。
气密试验应在耐压试验合格后进行,若耐压试验为气压试验时,则无需进行气密试验。气密性试验压力一般取1倍的设计压力。气密试验前,应使膨胀节两端固定,防止试验时膨胀节端部移动。在试验时,压力应缓缓上升,达到规定试验压力后保压10分钟,不得有泄漏现象。试验介质温度应不低于5℃。
在气密试验时,可采用以下方法检查是否泄漏。 1)
在焊缝、法兰等连接部位涂抹发泡剂(如用重量比为10%的肥皂水)进行检查。若有泄漏,该处会出现鼓泡。
2)
沉水检查。对于尺寸不大的膨胀节,通常将其沉没于水池中检查,根据有无气泡冒出,判断是否严密。
3)
在试验气体介质中加入1%的氨气,在外壁焊缝等处贴上比焊缝宽2Omm的试纸, 观察有无颜色变化判断是否渗漏。例如,用酚酞试剂浸渍过的试纸遇了氨气就呈现红色。 在进行气密试验时,也要有相应得的安全防护措施。
(3)应力测定
对于波形膨胀节,不论是采用U形波还是Ω形波,其力学状态都是比较复杂的,为了便于工程计算,在进行力学分析时,都对计算模型进行了简化,如U形波,不同的研究者,分别将其简化成直梁、曲梁、环板模型。当然,这些模型与实际状态是有一定差别的。为了研究波纹的应力状态和最大应力点位置,对其应力进行实际测量是必要的,这种分析应力的方法,简称之谓实验应力分析。目前应用较多的实验应力分析方法主要有光弹方法和电阻应变法,电阻应变法有精度高、数据处理简单等特点,但是只能测定构件表面的应力,所测应力也只是电阻应变片栅长范围内的平均应力值。关于应力测定的具体方法和要求,请参阅有关资料。
(4)刚度测定
膨胀节的刚度反映了产生单位变形弹性反力的大小,是重要的力学性能之一,在工程上,有时要求提供较为精确的刚度值,如将膨胀节用在汽轮机上时,要求较为精确。但是,目前提供的计算式是在简化了的计算模型上推演得到的,和实际情况有一定的偏差,而且计算值皆为弹性范围内的刚度,而膨胀节的工作状态往往会进入塑性状态,因此,为了准确地掌握膨胀节的刚度特性,进行实际测定是很必要的。有时用户也要求提供较为符合实际的工作刚度。
1)刚度测定方法
膨胀节的刚度可以在有关的材料力学试验机上进行测定,也可在有关的自制的试验机上进行测定,不管在哪种装置上测定,都要求能测定所加载荷并准确记录对应的位移,从而求得刚度。另外也可利用膨胀节的拉杆对波纹管加载,由电应变法测得加载后的应变,由应变求得拉杆上的应力,从而求得载荷值、在加载的同时,也测定波纹管产生的位移值;知道载荷和位移值,可求得刚度。
在自制的简易装置上测定刚度时,可以利用测力计或拉压力传感器测定载荷,同时用有关量具测定位移量,从而求得刚度。给出的刚度值应注明是单波刚度还是整体刚度,其单位为N/mm。
2) 轴向工作刚度的决定
膨胀节的波纹管在弹性范围内,刚度和位移是成直线关系的,当位移较大时,波纹管进入塑性区,就不再保持直线关系了。实测刚度时,在载荷--位移曲线上表现为位移较小时的各测点连线近似为直线,当位移较大时,就超过了波纹管的弹性范围,此时各点的连线就不再是直线了,如图52所示。
图52表示了波纹管轴向作用力和位移的关系,曲线D为轴向作用力和位移变化的实际对应关系,加载初期为直线,当位移增加到一定程度后则变为曲线。卸载时为直线,若反向进行轴向加载,可回复到初始位置,曲线A为按理论公式计算的结果,在位移较小时,和D曲线向吻合,由图可见,此时,若以A作为轴向刚度,则设计时给出的弹性反力会比实际大。若以连接00′的B线作为轴向工作刚度,则设计时给出的弹性反力都比实际小。若以连接O′E的直线C平移至C′作为轴向工作刚度,则给出的弹性反力值居于A和B之间,与实际值的偏差相对较小,但是与实际值还是有一定的出入。在工程设计中,可分析具体情况进行设计。
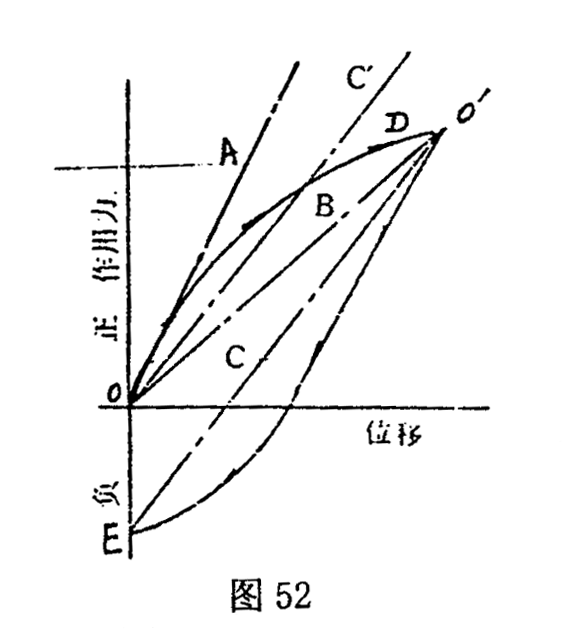
有些工程设计,需要准确地掌握波纹管的轴向工作刚度,此时,生产厂家应说明所提供的刚度的由来。必要时,需对实际产品进行测试,以便提供准确的载荷一位移特性。
对于有角向位移与横向位移的膨胀节,也可以利用轴向工作刚度分别计算由角向位移与横向位移所引起的力矩和横向力。
(5)稳定性试验
稳定试验的目的在于测定波纹管发生失稳时的临界内压值。试验中,根据波纹管的波距在内压作用下的改变量来确定是否发生了失稳。当初始均匀对称的波纹管在内压的作用下,各波纹之间不再保持平行,或相邻节圆对应点的距离出现长短不一时,即认为发生了屈曲,当内压作用所引起的最大波距与无内压时波距之比,对于无加强的波纹管超过了1.15倍,对于加强的波纹管超过了1.20倍时,则认为出现了失稳,此时对应的最大压力值即为临界压力。
在试验时,应采取措施使波纹管处于平直状态,同时要使两端固定,在试验中,端部不得发生任何移动。在进行稳定性试验前应测量各波纹之间的波距。
在进行稳定性试验时,波纹管轴线可以处于水平位置,也可以处于垂直位置。但是,对于水平安装且柔度较大的波纹管,最好在水平位置进行试验。试验中不应在外部对波纹管的波纹进行任何约束,除非这种约束是膨胀节整个结构上的零部件所造成的。
测定波距时,应在波纹变形最大的平面内测量。
在实际测试中,膨胀节应模拟实际工况给予固定。但是,对于承受横间位移和角向位移的膨胀节,也许不能明确确定真正的失稳界线。
进行内压稳定性试验时,试验介质一般为水。加压应逐级进行,每个级间压力差不超过设计压力的15%。并应逐级分别测量波纹管各部位的波距变化和中间1一2个波的横向挠曲位移。
(6)疲劳试验
当系统装置开停工操作或正常操作中的温度变化都可能引起管道及设备的热胀冷缩,从而也使波纹管产生伸缩变形。有些场合,也会因机械位移而产生伸缩变形。这些位移变化所引起的应力往往是交变应力。另外,操作压力的波动,也会引起交变应力。膨胀节在交变应力作用下就可能引起疲劳失效。对膨胀节而言因位移变化较大,所以引起的交变应力范围也较大,容易引起疲劳破坏,因此波纹管的疲劳已成为设计计算时必须认真考虑的问题。
关于膨胀节疲劳的设计计算公式或曲线,一般有两类:一类是为半经验的理论公式,如在曼森-柯芬公式基础推演而得的兰格公式就属此类。另一类是以实验数据为基础的公式或曲线,像EJMA(美国膨胀节制造商协会标准)标准中的计算式和曲线就属此类。根据实际应用情况来看,EJMA的计算公式和实际情况较为接近,但是各种设计公式或图线都是有一定适用条件的。同时,疲劳寿命的影响因素很多,数据也较分散,因此,为了实际考核膨胀节的抗疲劳性能或者为了检验波纹管可以承受预定的变形循环次数,进行疲劳试验是很有必要的。疲劳寿命也是考核膨胀节产品质量的一个重要指标。
1)试件
膨胀节疲劳试验的试件,一般应是实际产品。作为试件的产品应是有代表性的合格产品。试件的波数应不小于3个,波纹的波形及制造工艺应符合有关标准要求,试验前,应全面常握波纹管的各种参数。
2)疲劳试验条件的决定
疲劳试验应在专用的疲劳试验机上进行,目前常用的疲劳试验机有液压式或机械式两类。
对于设计温度在材料蠕变温度下的膨胀节,试验可在常温下进行。
在进行疲劳试验时,波纹管内可以是常压,也可以是采用变化的压力。后者更接近于膨胀节的实际使用工况。其循环位移可以是拉压对称位移循环,也可以是从自由长度进行轴向压缩至规定值的位移循环。决定循环试验速率时,应使位移在各波间能均匀地分配为原则,一般以每分钟不超过30次为宜。
疲劳试验中,当波纹管出现了穿透性裂纹时,即认为已发生疲劳破坏。此时测得的循环寿命,即为膨胀节的实际疲劳破坏寿命(次)。
在疲劳试验中各波的变形可能不一致,要注意观察各波距的变化。在进行疲劳破坏寿命计算时,可根据各波距循环位移的实际测量值和波纹管的实际尺寸进行。同时,为便于分析,也要根据图样上的名义尺寸进行计算。最后列表进行比较。
(7)膨胀节的爆破试验
膨胀节有可能由于结构设计不合理,制造质量不符合有关标准要求,或操作不当等原因而引发爆破。发生爆破时,往往会给生命财产造成巨大损失,因此膨胀节发生爆破的问题,也被工程所重视。
1)加压时U形波纹的变化过程
膨胀节爆破试验装置和液压试验装置基本相同。因为是爆破试验,应十分注意安全问题。膨胀节爆破试验时,在不断加压的过程中,膨胀节波纹管的变形大致过程如下:当压力逐渐升至设计压力时,波纹管外形无明显变化。当压力继续升高,波纹管会出现失稳现象,可能是平面失稳,也可能是柱失稳。当直径较小,波数较多时,即L/D比值较大时(L一波纹管长度;D一波纹管直径),往往会发生柱失稳。否则,可能发生平面失稳,当出现失稳后,继续加压,此时,波谷可能部分地被压扁。压力继续上升,失稳加剧。再继续加压,则波纹管产生明显周向鼓胀,并会发生波形局部明显鼓出,波谷也被拉曲。内压再继续升高,最后会发生爆破,爆裂口一般应是沿经向的。此时可从压力表上读出最终的爆破压力,一般爆破力还是较高的,可达设计压力的5倍,甚至更高。
2)U形波纹管膨胀节爆破压力的计算
U形波纹管在加压过程中,形状变化很大,很不规则,而且其变形形状受长径比等参数的影响较明显,因此还没有建立较完善的爆破压力计算公式。在此推荐按式(72)计算爆破压力:
Pb=[(1.14q+4h)δmmσb]/[(Db+2h)q]
(72) 式中 q--
波距,mm; h--
波高,mm;
Db--波纹内径,mm;
δm--不锈钢波纹管一层的实际厚度,mm;
m-- 波纹厚度δ的层数:
σb-- 材料在操作温度下的强度极限,Mpa;
爆破压力测定结果和计算结果见表2。
|